Powder coating surface defects result in rejects. Rejects from coating lines can come from a substrate defect, a surface contaminant or a coating material defect. Process controls should be implemented upstream of the coating line to prevent a defective substrate from entering the line.
If a substrate is defective and has entered the coating line, it is important to recognize the source of the blemish and not waste time trying to fix the coating process to correct a pre-existing substrate condition.
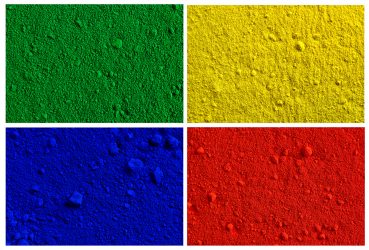
Big collection of colorful powder – yellow, red, green, blue
Dirt on the surface of a coated part is a major concern for all coaters.
Dirt may come from the air around the spray environment, from the application equipment or it may be in the coating material.
If a defect is from contaminated coating material or manufacturing byproducts that have not been removed by the cleaning process it will be evenly distributed and, if it is an external source, the defect will more likely be random.
Dirt in a powder coating can be screened out. Rotary sieves or vibratory sieves can be used to filter power fed from the collector module.
Integrated screeners can be built into collector modules. Even an all manual operation can screen powder by putting it through a stainless steel screen before loading it into the feed hopper. Powder should always be screened.
Reclaim needs to screened to eliminate dust that has entered the booth. Virgin material should be screened to make sure that there are no chips or contaminants in the box.
Dirt from ineffective pretreatment can usually be corrected by changes in the process or control of the pretreatment system. Soils that are on the part from the manufacturing process that cannot be removed by a spray washer can usually be tracked to the source so a change can be made to eliminate them.
Air borne contaminants are the hardest to track and eliminate because they can come from so many different sources. Keeping a clean environment around the system is one of the best ways to reduce air borne dirt.
Electrostatically applied powder can contain airborne dirt and deposit it on the parts.
For the best powder application once your part is as clean as you can get it, check out Polifluid Powder Coating Technology from Coating Delivery Technology, Inc.
Control airborne contamination
The list below names some of the common sources of airborne contamination.
- People – Air sampling of enclosed coating systems has shown that as much as 80% of the airborne contamination comes from the clothing, hair and shoes of personnel.
- Nature – Pollen, road dust and other outdoor dirt are sometimes brought into the plant through doors, windows and unfiltered air supply systems.
- The Building – Concrete floors may wear and give off dust.
- Manufacturing – Mechanical operations in the manufacturing process may generate dust, metal shavings, or wood dust.
- Process Equipment – The conveyor, the oven, the washer or other operations within the coating line can generate or concentrate dirt that will create a defect.
Screen your reclaimed powder
One of the beauties of powder coating is that there is very little wasted material-whatever powder doesn’t adhere to the part falls to the floor of the spray booth where it can be collected and reused. Unfortunately, particulate or dirt can be collected along with the powder, often building up within the reclaim system. “If the powder is going to be recycled for reuse,” Rodger Talbert explains, “the reclaim system will route the powder back through a sieve or screen designed to remove any built-up fibers or particulate and deliver clean powder to the feed hopper.”
Typically, an 80-mesh screen (meaning 80 holes per square inch) is used to filter particulate from the powder. Powder particles are typically 35 to 45 microns in size, but can be as large as 100 microns. A higher mesh screen, Talbert cautions, could become clogged or plugged up, since the powder particles won’t be able to pass through. “You’ll waste a lot of powder; the screen will take it out [of use] and you’ll have to throw it away.”
***Read Pinholes And Outgassing: Troubleshooting Your Powder Coated Finish from Reliant Finishing Systems.
Powder Coating: Good contamination control prevents defects from start to finish
In order to ensure that a powder coating operation is producing the highest quality, defect-free finish, however, certain steps must be taken to incorporate basic contamination-control techniques into the finishing process.
Keep it clean!
The first line of defense against a defective powder-coated finish is the pretreatment process. “In powder coating, your finish is only going to be as good as your pretreatment process,” says Jeff Hale, manager of distribution and marketing for well-known powder-equipment manufacturer GEMA (Indianapolis, Ind.; www.gemapowdercoating.com).
The first step is to clean the part, usually with a spray washer and an alkaline cleaner, to remove any organic soils-dirt, waxes, or rust inhibitors-that may be present on the substrate.
However, Inorganic soils, like rust, oxidation, mill scale, or heavy mildew, may be difficult to remove with a spray washer, notes Rodger Talbert, president of R. Talbert Consulting (Grand Rapids, Mich.; www.talbertconsulting.com). “If you have problems with those kinds of soils, you can either chemically treat the surface with something more aggressive than the typical spray-washer solutions, or you can mechanically remove the soils by grinding, polishing or blasting.”
If the substrate has not been cleaned well, Hale explains, then the powder coating may not adhere to the surface…any contaminants-smut, dirt, or oil-left on the substrate, he warns, can cause the powder to flake or peel off later.
Once the part has been cleaned, it is rinsed in water or deionized water. In some applications, where corrosion resistance is not a concern, this is the extent of the pretreatment process. For instance, a fence post doesn’t require the high level of corrosion resistance as, say, a washing machine. The household chemicals and detergents that will come in contact with the powder-coated surface are basic in pH, GEMA’s Jeff Hale explains, while other cleaners that might be used to wipe up dust and spills on the appliances can be more acidic. The powder coating must be able to resist that. “Let’s say there’s a crack in the coating,” he suggests. “There needs to be a level of pretreatment underneath the coating to protect the metal from rusting or corroding.”
In such cases, the substrate will undergo a phosphatizing process-called a conversion coating-whereby an acid solution is used to attack, or etch, the surface of the base metal. The solution-usually iron phosphate or zinc phosphate-provides a layer of improved corrosion resistance and strengthens the adherence of the powder coating to the substrate. As Hale explains, “Phosphatizing is a way to lay a conversion coating over the substrate-a barrier between the raw metal and the powder. [This] gives the powder coating something to ‘dig its fingers into,’ if you will.”
The trend now is toward non-phosphate pretreatment.
See this article: Phosphate-free Metal Pretreatment for more information on this.
Cool the part before applying the powder coating
“Hot parts attract powder more readily,” says Hale. “The hotter the part is, the more likely you are to apply excess powder.” Excessive temperatures, he explains, can cause a premature melting of powder particles on the substrate, causing the powder to become tacky. As more powder is sprayed onto the part, it adheres to the tacky spots and builds up, resulting in uneven coating thickness. This can affect not only the aesthetics of the part, but the ability to assemble it. More powder also means wasted product, and can result in a significant increase in materials cost.
Ideally, these parts need to be cooled down to below 100°F in order to effectively control the thickness of the powder coating. If a part is allowed to cure at the plant’s ambient temperature, be sure the ambient temperature is itself relatively cool.
In more sophisticated systems, however, a cooling tunnel is used to quickly and effectively cool parts. A cooling tunnel is simply an uninsulated sheet-metal tunnel in which filtered outside air is directed across the parts with large fans.
Control the humidity
Powder is extremely sensitive to moisture; excessive humidity can cause the powder to agglomerate, or clump. Consequently, the ability to spray the powder consistently and fluidly is compromised, causing little spits or balls of powder that can clog the pump and other equipment. Ideally, The Powder Coating Institute recommends powder be stored at 72 to 75°F and 50-60 percent relative humidity. If the humidity is too high or too low, sometimes the powder goes on clumpy, or too thin, or it won’t stay on the part long enough to even make it to the oven.
Excessive humidity, and excessive dryness, can also cause problems with your electrostatic gun, making it difficult or impossible to impart a charge to the powder particles as they are sprayed.
Too much moisture in the air doesn’t allow conduction of the charge onto the paint particles as they pass through the ionized airfield. If it’s too dry, there’s not enough moisture for the process to work either.
Use an “E-room” (environmental room) to cut down on defects
An environmental room-or E-room-is a controlled environment that houses the actual powder coating spray booth, allowing manufacturers to reduce or even eliminate defects in the powder coating finish by controlling the variables that can cause problems.
Jeff Hale says, “As we’ve told customers, if they want to minimize the headaches they have in terms of material handling or ‘sprayability’ issues, we strongly advise that they look at an environmental room.” Hale acknowledges that if a customer does not invest in an E-room, it doesn’t mean that they can’t powder coat; it just means that, during hot, humid summer months for example, they must be prepared for increased material-handling challenges.
***For more information on E-rooms, see PCO page Modular Buildings|Partitions|E-rooms
Store your powder properly
Properly stored powder can prolong its shelf life, and possibly reduce contamination issues further down in the process. As mentioned above, The Powder Coating Institute recommends storing powder at less than 80°F and in 50 to 60 percent relative humidity. In addition, powder should be stored away from a heat source, such as an oven, washer, furnace, or space heater to keep it from prematurely melting. PCI also advises that boxes of powder should never be stacked on top of one another; this can result in lumps that are not easily broken.
Summary
With all the potential sources of contamination that can cause defects in your powder coating, the job of coating a part with no defects is a challenge to say the least.
The level of dirt prevention that an operation adopts is directly related to their quality standards.
Although contamination can threaten a perfect finish, incorporating some basic contamination-control techniques into the manufacturing process can drastically reduce, or even eliminate, coating defects.
Related Resources
pcoadmin